Projects
Drying Systems and Dust Collection
Matrix has extensive experience with dust collection system including many difficult and combustible dusts. Matrix has even custom designed and supplied collectors for special purpose or tight/awkward spaces. Our drying experience spans rotary kilns to fluidized beds to spray dryers. Dryer designs include CGMP and sanitary applications.
Matrix Engineering was asked to help solve material storage problems due to the hygroscopic nature of Carbopol. Matrix provided the mechanical engineering necessary for designing a new bin vent and DRY nitrogen purge arrangement that vented the hopper only when necessary and cleaned the filter bags only when dirty. Matrix also provided a bin discharging aeration system for eliminating and/or preventing bridging problems. In addition, Matrix provided the control sequence and electrical engineering necessary for operation of the bin vent and aeration discharge system in a Class I Div 2 Group D and G environment.
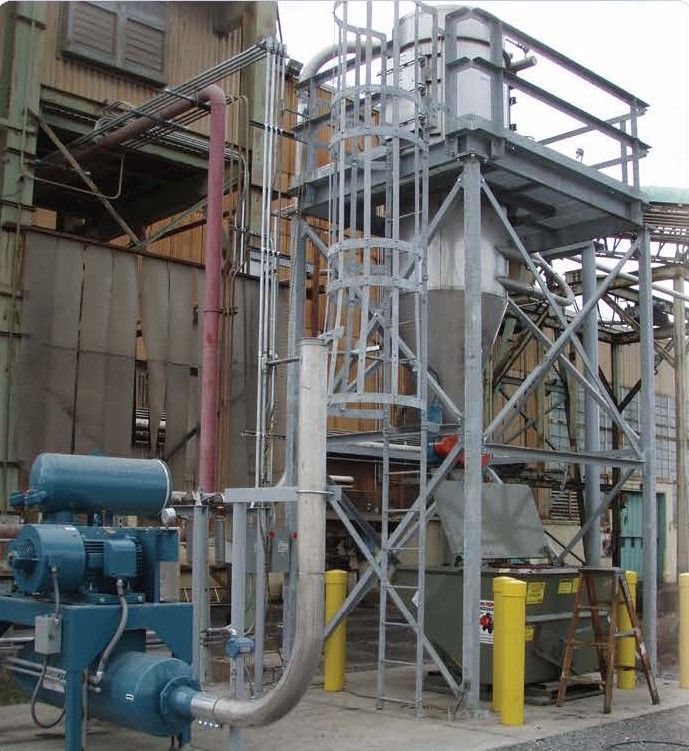
Matrix Engineering performed the mechanical, electrical and control system design for a central vacuum system for primary handling of coal dust. The system has over 50 hose pick-up points in 2 different zones with over 250 ft convey distance required. We designed a 2” hose system at 14” Hg for maximum performance.
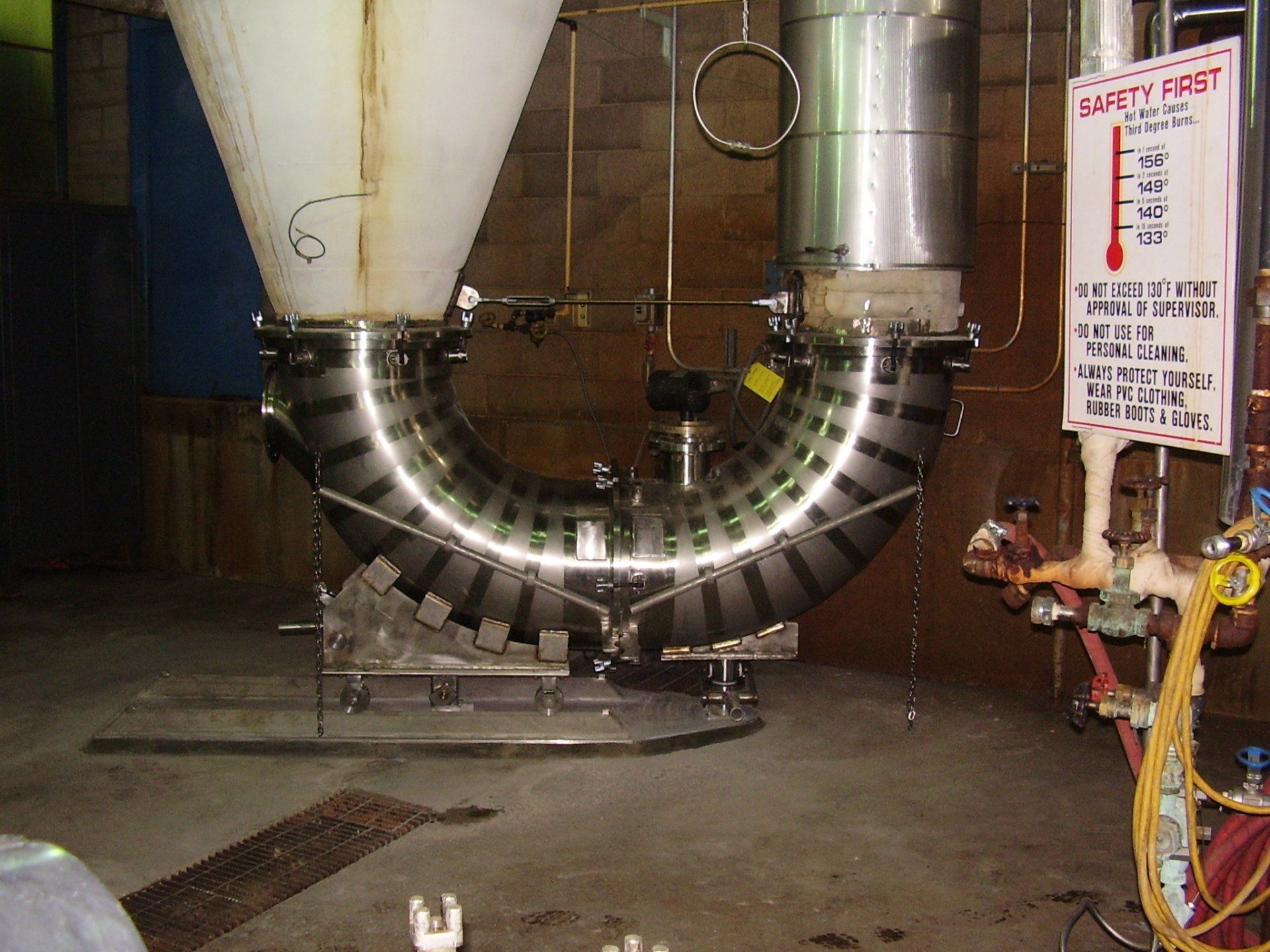
Matrix provided the mechanical design for custom design of a sanitary u-bend at the bottom of an existing spray dryer. The u-bend had to be dis-assembled and cleaned frequently for product changeovers. Our sanitary design allowed for quick and easy cleaning by rolling back half the u-bend on a track and rotating the other half on a pivot bearing. Not only did the tool-less design provide ease dis-assembly and assembly, but it also provided a superior o-ring seal over the previous arrangement. This is extremely beneficial for a vacuum system handling a glue-like powder that is seeking moisture. Our design substantially reduced product build-up between cleanings and allowed viewing of operation and status with a properly positioned viewport and light.
Matrix provided the structural, mechanical and electrical engineering required for the production of a new leavening powder in an existing process. Major modifications were required to an existing air blending and conveying system and a new separate dust collection system was required to avoid cross contamination between the different products. The dust collection systems for these products was very sophisticated. Simultaneous operation was required for on both collectors for the packaging of one product while another was being produced. This simultaneous operation had to be accomplished with cross contamination adding a high element of complexity to the control system. Matrix provided the engineering for a new control system for the blending, conveying, packaging & dust control system. Matrix also provided total commissioning/start-up support for this system. There were also considerable spatial constraints for introducing this new product to a well established process area. However, we were able to squeeze our new production surge hopper between existing storage and packaging bin to utilize existing blending and dense phase systems.

Matrix provided the structural, mechanical and electrical engineering required for a 3500 cfm fugitive dust collector in a Class I Div 1 environment. The dust collector provided central dust collection for several packaging systems as well as a specially designed hood for an adjacent air pallet unloading station.