Projects
Industrial Buildings & Process Structures
This is a small sampling of our many structural projects in industry. Our designs include Process Buildings, Open Structures, Sanitary CGMP Designs, Bulk Material Handling Supports, and many others throughout many Industrial Sectors.
Matrix Engineering was employed to provide the civil, mechanical, and electrical engineering necessary to build a 29,000 sqft factory and office facility. Matrix provided the site work, architectural, foundation, HVAC, natural gas piping, plumbing, lighting, electrical power and computer network drawings. The office portion of this factory was over 5500 sqft.
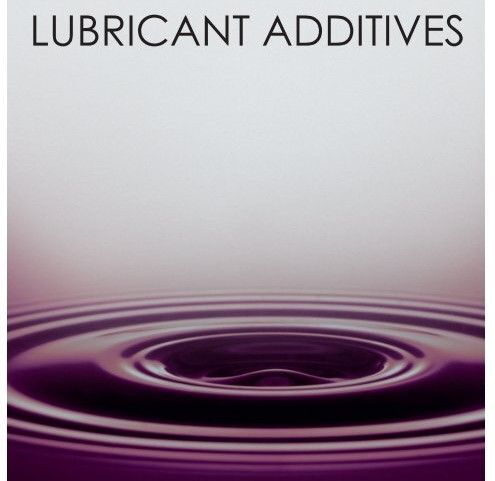
Matrix provided the civil, structural and mechanical design for a major addition to the existing Vanlube process at Vanderbilt Chemical's Murray, Kentucky facility. The product was a NFPA 30 Class 1B flammable liquid requiring special design considerations for firewalls, escape routes and equipment placement. The project consisted of a process area, packaging area, tank farm and truck load-out facility. Mechanical design included heating and proper ventilation per NFPA guidelines. Matrix also provided all of the complex grounding details and electrical classification drawings to satisfy the NFPA guidelines.
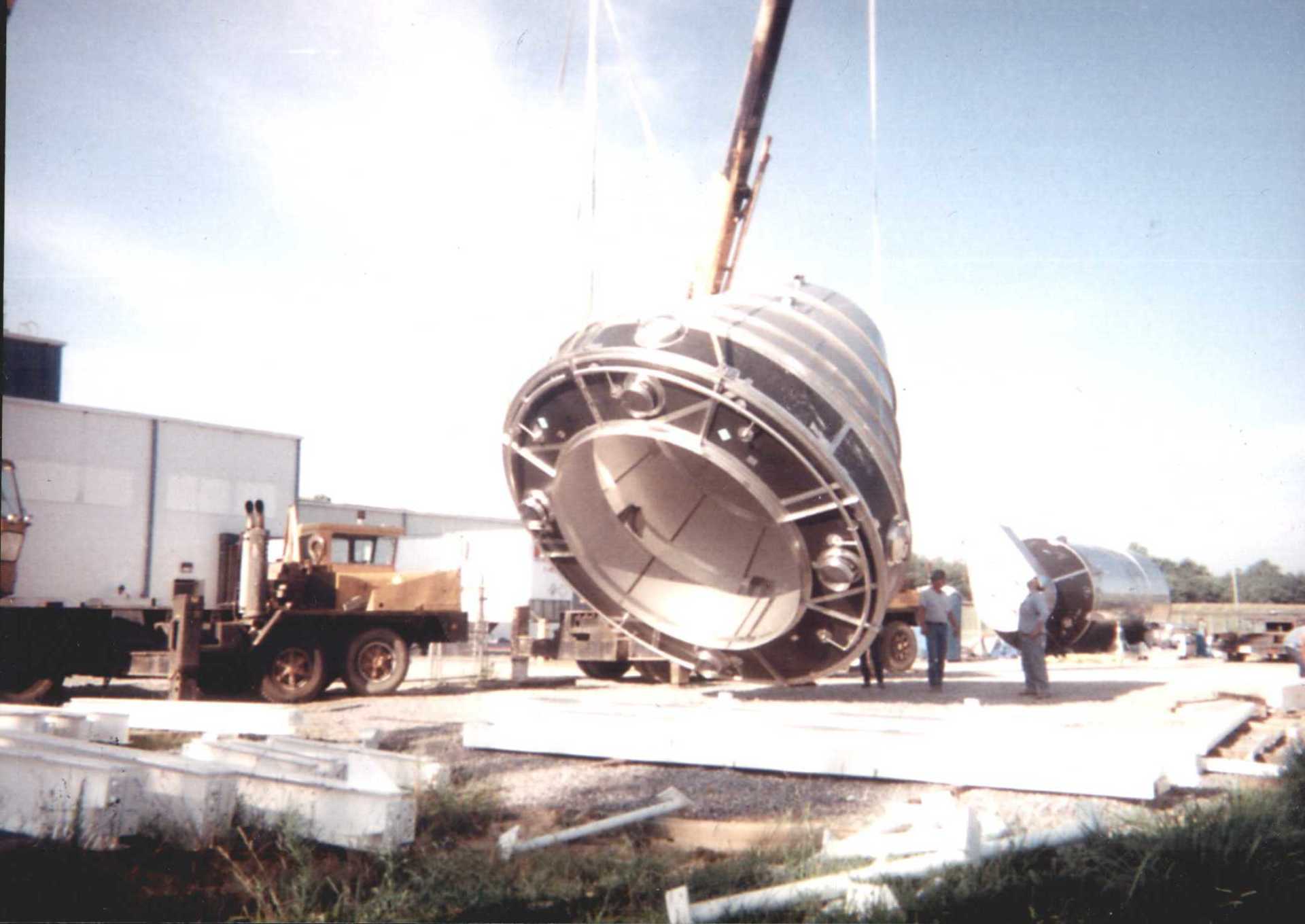
Matrix Engineering provided civil, structural and mechanical design for a spray dryer facility used in the production of pharmaceutical clay. Matrix assisted in the facility layout by coordinating the client with the spray dryer equipment manufacturer as well as the structural requirements of the seventy feet tall, 5-floor structure. We also designed a large versatile mechanical ventilation system for keeping the work environment bearable around a hot process during the summer months. In additions we engineered the sanitary dense phase pneumatic conveying systems for moving the powdered clay around the dryer facility as well as pneumatic blending to homogenize batch campaigns. Twenty years later, Matrix was recalled to design and build a twin facility with a new spray dryer right next to this one.