Projects
Packaging and Palletizing Systems
As a part of our powder handling expertise, Matrix has designed and helps to maintain many different packaging systems, from drums, IBC's to bags Matrix can custom design or specify new system or improve an old one.

Matrix Engineering provided the structural, mechanical and electrical engineering for a drum packaging improvement project at ISP. The previous drum filling operation was manual and labor intensive requiring tipping and manhandling of 600 lb drums. The product in this case was an additive for hair spray which is responsible for its stickiness. The product is very viscous with the consistency of a very thick syrup that dries like glue. Matrix conceptualized and designed twin drum filling lines in which empty drums are palletized and filled on a scale. Loading arms for filling drums were designed to swing to either pallet scale for versatility in loading drums in either drumming line from two different tanks. Our engineers designed the piping systems associated with the product as well as caustic piping required to backwash the system and clean it out after packaging runs. We also designed an quick-acting air operated swing door system for accessing each scale with a fork lift. This area was also a Class I Div 2 area.
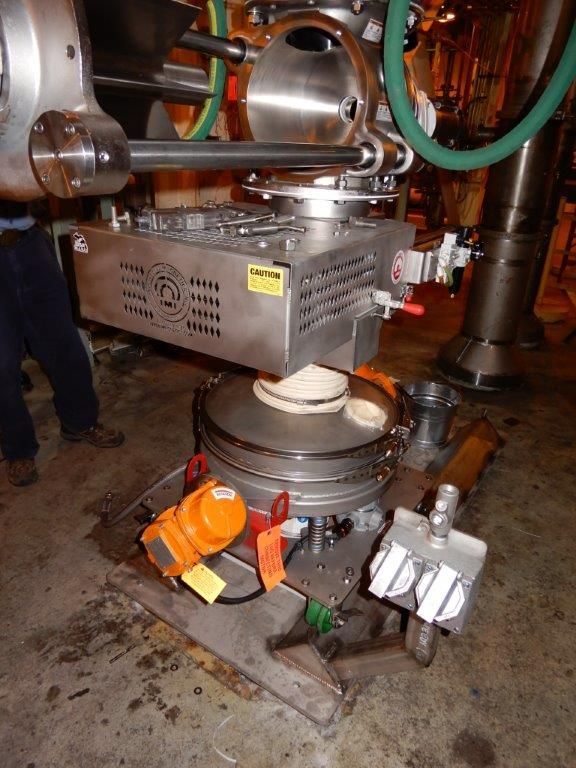
Matrix performed all design engineering and control integration required for a pharmaceutical grade packaging system including a sanitary and clean-in-place design for discharging the product from the packaging bin. Downstream equipment included a sanitary airlock, magnet, screen and metal detector. We replaced a vibrating bin discharger which was impossible to thoroughly clean and inspect with a sanitary aeration discharge cone. The airlock had a removable rotor that slid out from the housing on linear bearings. In addition we were able to mount the vibrating scalping screener on a stand with v-groove wheels for ease of pulling out of the stack-up for cleaning and/or screen changing. The system was so well received, we have since duplicated in other processes for this same client.

Matrix Engineering provided mechanical and electrical engineering for a temporary bulk bag filling system in a Class I Div 2 environment. Changes were necessary in the existing packaging system yet the production of the product was sold-out and needed to continue. Matrix helped devise a way that could be implemented quickly to divert the production stream into bulk bags for re-packaging at another location.
Matrix Engineering provided mechanical and electrical engineering along with controls for a sanitary drum filling system in a Class I Div 2 environment. The mechanical engineering package included detailed design of the drum fill head for an inflatable seal and improvements in dust control during filling. A smooth bore flexible connection was custom designed to prevent ledges for product to rest. A batch fill weighing control system with HMI was designed for filling within 0.2 lb on a 110 lb drum. The drum filling system had be recently replaced by another firm and was unable to consistently hit the target weight tolerance. Matrix responded immediately with a retrofit design that met the specification and satisfaction of the plant engineers and operators. Over the years, Matrix maintained this system with check scale upgrades, automated fill and check conveyors, as well as a powered accumulated drum staging conveyor.
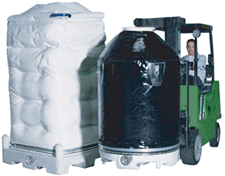
Matrix Engineering provided the structural, mechanical and electrical engineering for the addition of an air pallet fill stand to an existing box packaging system. The product handled was very hygroscopic as well as overly free flowing - capable of bridging the discharge or flowing uncontrollably. We used a positional butterfly valve on the packaging bin discharge with a control loop to position the valve based on the throughput rate from the fill stand scale. Level instrumentation was also used for preventing material from backing up in the delumping mill. Much of the complexity of this project involved sizing an incline screw feeder between the hopper and fill stand large enough to handle instantaneous flooding with control logic to watch and adjust the average throughput to keep the screw running in the 15% - 30% full range. This helped to minimize the challenge to the inlet end seal on the screw conveyor.
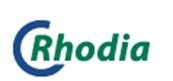
Matrix performed preliminary belt conveyor and equipment layout with specifications for a dual product palletizing system. Duties also included palletizer system evaluation including systems by Slidell, Mollers, Stone, PSI, and PASCO. Matrix performed preliminary design of a building extension to house the proposed palletizer. Matrix engineers also helped prepare estimates for total project cost as well as project schedule. Over the years, Matrix added new features to the palletizer system including bag printers, metal detectors and reject offramp conveyors. Matrix handled the mechanical engineering for these projects as well as maintaining the old AB PLC5 controls programming for the system.
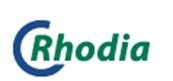
Matrix provided the structural, mechanical, and electrical engineering necessary for providing a dry storage, unloading and empty drum magazine storage for an existing P2O5 drum filling operation. Phosphorus Pentoxide is very hygroscopic forming hot phosphoric acid when it encounters water. Therefor packaging with wet drums stored outside caused a significant problem. The design consisted of a semi-trailer unloading dock where trailers could remain parked while keeping mobile dry drum storage out of the weather and could be unloaded as packaging campaigns dictated. Gravity conveyor magazines were designed so that an operator could unload enough drums out of the truck trailers for. This arrangement also saved labor since it eliminated "double handling" of the drums.