Projects
Control System Design
Matrix designs and builds Controls Systems for Industrial, Manufacturing and Marine Clients. Matrix has a UL Listed 508A panel shop for industrial controls. We also have the UL Listing 698 for providing power and signals safely to an XP environment.
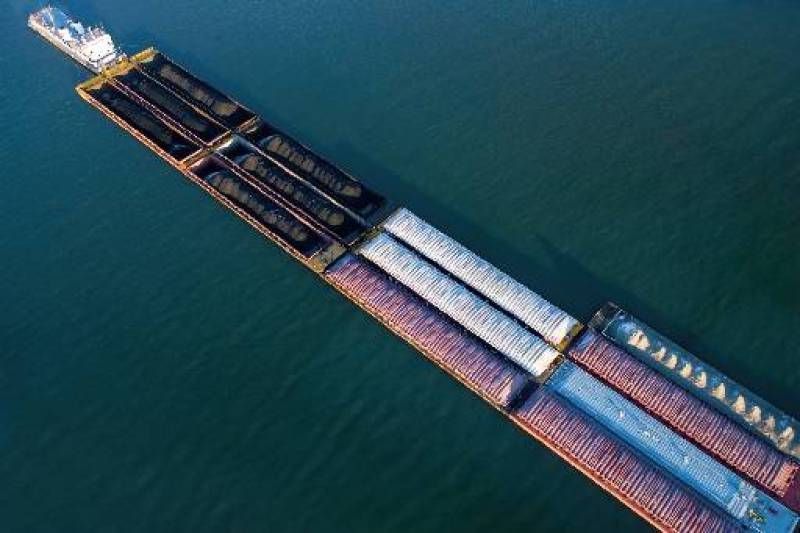
Matrix Industrial Systems provided all hardware and PLC programming for a barge positioning system used for loading and unloading barges without assistance from a tugboat. The control system included 2 VFD’s, one controlling a winch on the bow of the barge, the other on the stern. Our control system adjusted tension on both winches to balance and position the barge.